Does your supply chain keep you up at night? Due to ongoing market disruption, companies’ risk exposure has never been greater. Now is the time to design supply chains that can overcome risk today and thrive in the future.
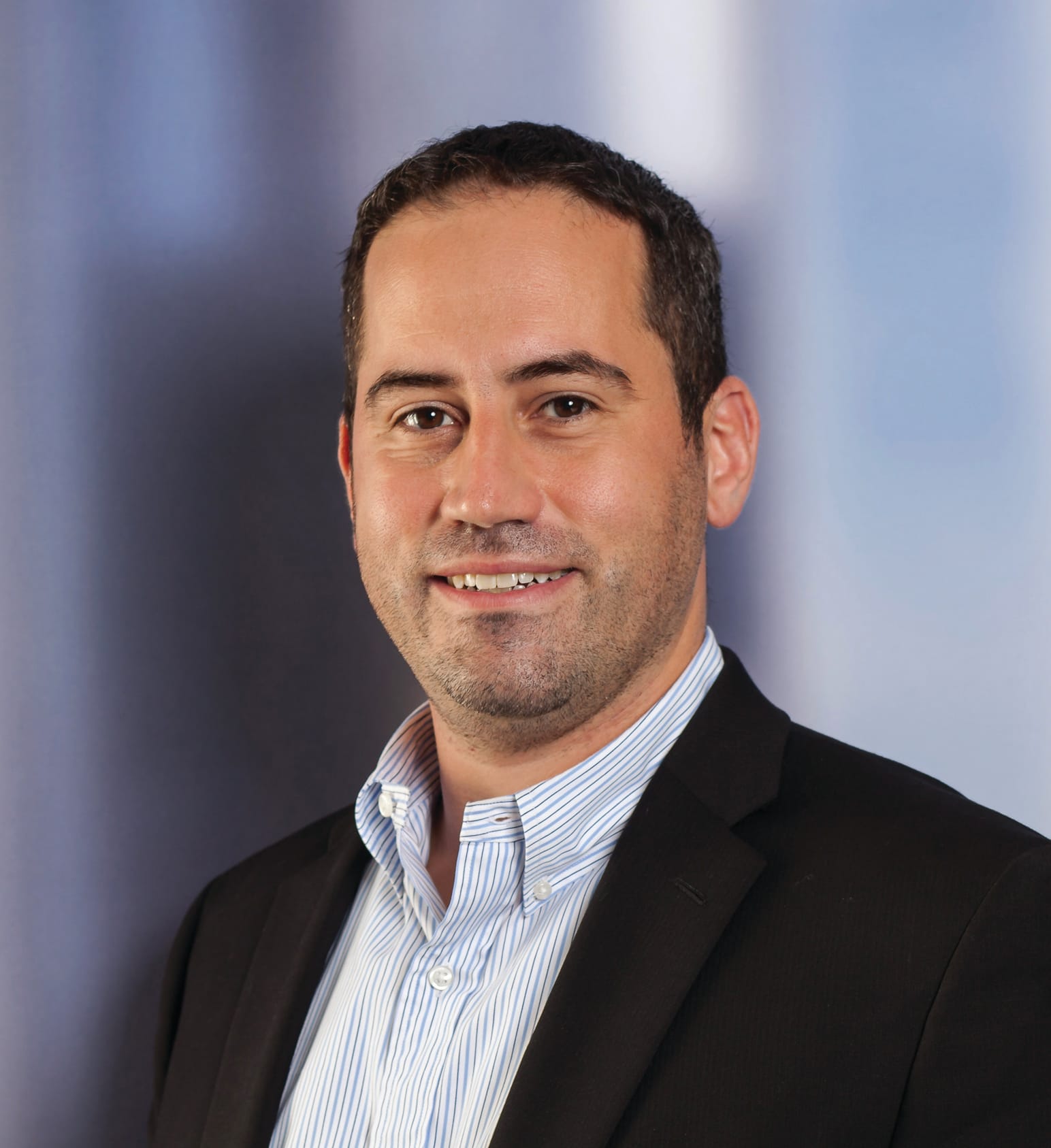
Mike Piccarreta
COVID-19 illustrated the vulnerability of supply chains to significant demand shifts and supply shocks caused by geopolitical tensions, localized regulations and sole-sourced suppliers. During these challenges, companies’ typical safety nets — conservatively designed networks and well-funded safety stocks — have proved ineffective.
Those supply chain disruptions have significant financial impacts. In Fortune 500 companies, supply chain incidents caused an average of $2.4 billion in market cap decline; supply chain disruption caused an average of $450 million in revenue losses and $75 million in excess COGS expenditures per year. So it’s clear the stakes (companies’ reputations, revenue, goods sold) are high.
Looking ahead, both pharmaceutical companies and chain drug retailers need to reimagine their supply chains. By implementing innovative risk management strategies, companies can proactively address modern challenges and create resilient supply chains that are ready for the future.
Supply chain disruption has forced a new approach
Pandemic-fueled disruption in the supply chain isn’t new. We’ve been experiencing incredible disruption and challenge for three years now, and every supply chain leader has undergone countless trials and tribulations. As a result, we have years of data to reflect on to understand companies’ actions and results. At first, there was major panic as companies tried short-term, reactionary fixes. Then, companies built manual solutions that were slow, expensive and unsustainable.
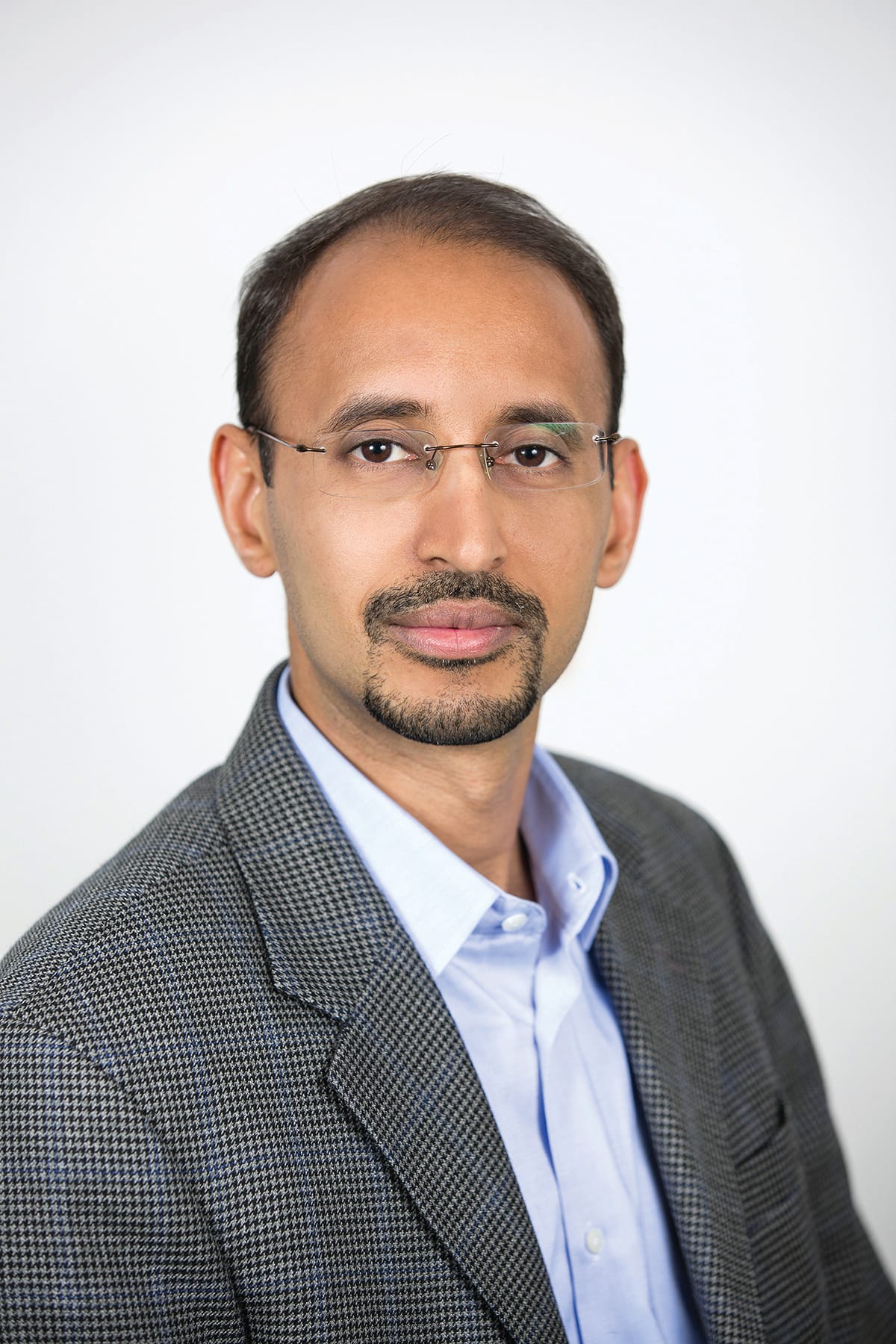
Vishal Bhandari
As the disruption stuck around, supply chain leaders turned to technology to fix supply chain woes. Many companies bought off-the-shelf technology solutions to solve their supply chain problems and prepare for the next wave of disruption. But those investments haven’t always borne fruit. Point solutions often add to the noise and don’t create a connected, end-to-end ecosystem.
At this point, those risk mitigation efforts are starting to mature. Companies are seeking solutions customized to their business as they realize that off-the-shelf tech alone doesn’t solve the problems in the supply chain. Instead, the best solutions bring together technology, artificial intelligence and human intelligence to solve these supply chain challenges, as the savvy leader takes a new, more creative, complex approach to craft resilient supply chains. It involves linking technology to business processes, informed by a steady influx of data, to predict and solve for disruption as it emerges.
A data-driven approach to supply chain resilience
The sustainable solution to these supply chain disruptions is to build a connected, end-to-end system that senses risk throughout the value chain and ensures the risk gets closed. Utilizing the 4-step SIPE process outlined below, we can sense and mitigate risk across the value chain.
- Sense: First, improved resilience starts with robust sensing capabilities that enable companies to detect possible risks preemptively and proactively act. To make informed decisions, leaders need to bring in all relevant data (from external data like news feeds and financial health to internal data like supplier performance indicators, inventory levels and bills of materials) to build a risk fact base.
This sophisticated sensing requires an increased breadth and depth of data and analysis to monitor and evaluate a comprehensive set of risk indicators. Although most companies track financial risks and some operational risks, leaders are expanding their scope to monitor potential threats in cybersecurity, ESG and geopolitical risks that could disrupt the supply base. In addition, upstream supply chain visibility for tier 2+ suppliers is crucial since risks can reverberate across the value chain and are often overlooked.
- Illuminate: Sensing the data is just the first step. Building that risk fact base informs the next step: analyzing and prioritizing risks. A cognitive risk engine ingests and synthesizes collected data sources. Then, advanced analytics and AI develop predictive insights, translating the data into risk signals and business impact.
Teams consider how the risk will impact the value chain and assess the potential impact to the organization in order to prioritize actions. Novel machine learning techniques can come into play here, conducting scenario analysis, highlighting the potential impacts of risks and generating predictive insights to support decision making.
- Plan: With the risks defined and prioritized, teams can create a plan and validate potential actions. Supply chain teams are setting up cross-functional digital war rooms to triage risk, evaluate trade-offs and prioritize actions, bringing the end-to-end strategy needed to avoid or minimize disruptions to the business. Teams ask: What do we continue to monitor? What should we act on now? Which risks can we address further down the road?
Those answers determine the mitigation action. Mitigation actions are pre-planned and tested and are connected to downstream business processes.
- Execute: Finally, in the execution step, supply chain teams are informed and ready to track and monitor action plans and develop strong workflow management to ensure those actions are executed.
We use a connected tool to track actions and ensure users are notified when they need to act. The tool also provides real-time insights into how risk is being reduced and actions closed to provide feedback to improve performance.
That powerful feedback loop continues to run through the SIPE cycle, making the risk-sensing and prioritization system more and more powerful.
For example, one big pharma company used a supply resilience framework to get new products to market.
The company had more than 100 drugs in its R&D pipeline. A shortage in R&D materials and services had almost hampered R&D activities, reducing the pace of innovation and bringing new products to market. Frustrated with the existing firefighting approach, the team sought to develop a sustainable resilience operating model enabled by a strong technology backbone to sense and mitigate risk.
Using the SIPE model, the company developed a comprehensive solution to address current supply risks — and put into place a digitally enabled operating model for managing future risk. They designed a supply resilience framework, developed a technology plan and embedded supply resilience into the organization — the result is an end-to-end supply risk resilience platform and the governance to oversee it. These changes resulted in increasing the pace of innovation and improving speed to market for drugs in the pipeline.
A new way forward
Companies that invest in new approaches will find themselves prepared to overcome the near-term challenges of supply chain disruption — and thrive in the future.
Three final ideas to help supply chain teams anticipate disruptions and mitigate risk:
- Move to a more sustainable operating model for managing risk. Now that the most intense period of supply disruption has calmed, it’s time to revisit the choices made in the heat of the crisis and ask: What worked well that we want to strengthen through a more formal operating model and digital enhancements? What were the quick fixes that we can retire now? How can we make risk mitigation sustainable in our operating model?
- Instill a risk-aware culture and governance that works top to bottom. Aim to embed a risk mindset into the organization from top to bottom for proactive risk management.
- Deploy digital solutions to enhance the process and outcomes. Consider how choosing the right SCRM technology design could improve the end-to-end supply chain, from risk sensing to workflow management. Leverage digital technology as a backbone to support the operating model. Make informed choices on where to start and how to build versus buy to deliver the most value.
Mike Piccarreta and Vishal Bhandari are partners in the Healthcare and Life Sciences practice at Kearney, a global strategy and management consulting firm. They can be reached at mike.piccarreta@kearney.com and vishal.bhandari@kearney.com.