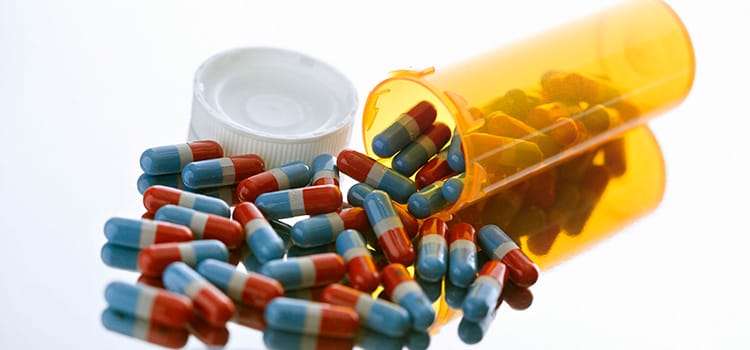
ARLINGTON, Va. — Reverse distribution of pharmaceutical products accounts for 3.5% to 4% of all pharmaceutical sales — more than 120 million product units — and exceeds $13 billion in value, according to a new report from the Healthcare Distribution Alliance (HDA) Research Foundation.
Reverse distribution involves moving unsold salable inventory within, or removing unsalable inventory from, the pharmaceutical supply chain. It is a complex, yet safe and secure, process that involves various supply chain stakeholders to manage products, all while complying with federal and state regulations.
Primary research for the report, titled “The Role of Reverse Distribution,” was conducted by Kindler & Crimmins Associates, and Bradford Rx Solutions. They interviewed key industry stakeholders and surveyed reverse logistics providers. The publication is sponsored by PharmaLink Inc. and Guaranteed Returns.
“Though forward distribution has been widely studied, we recognized there was a lack of an up-to-date, singular resource to describe the intricacies of reverse distribution,” said Perry Fri, executive vice president of industry relations, membership and education for the HDA and chief operating officer of the HDA Research Foundation. “Given the significant volume of returns in the pharmaceutical supply chain, the foundation is pleased to offer a comprehensive analysis of this process, while underscoring its effectiveness to the health care industry.”
The report describes the differing types of product returns — including delivery damages and mis-shipments; salable, unsalable, recalled products; and consumer-initiated returns — while illustrating the corresponding reverse distribution process and the key stakeholders involved. The analysis also highlights opportunities to enhance current return practices — through increased data and information sharing, by eliminating redundant operations and by increasing the use of electronic data interchange (EDI) to improve the reconciliation process.
As noted in the foundation research, legislative and regulatory changes affecting pharmaceutical reverse distribution might have a negative impact on the ability to process returns; even a small increase might add significant costs and increased levels of unsalable product returns. However, implementation of the Drug Supply Chain Security Act (DSCSA) may pre-sent an opportunity to enhance regulatory compliance.
“As regulators, such as the Environmental Protection Agency, reassess the process of disposing and handling pharmaceutical waste, the foundation report is a useful primer for those unfamiliar with the supply chain to understand the steps and stakeholders involved to efficiently manage pharmaceutical returns,” said HDA president and chief executive officer John Gray.
The report concludes that there will always be a need for an efficient and cost-effective reverse distribution function to help dispensers and wholesale distributors with managing excess inventory and providing a regulated, efficient process to safely and securely move (or remove) returned pharmaceutical products.
While there are clearly opportunities to cut unnecessary and redundant costs, the current reverse distribution supply chain is effective, the report says. But the reverse distribution industry faces future uncertainty, which may present challenges and obstacles.
The lack of an efficient and cost-effective salable return process likely would lead to increased levels of nonproductive and excess inventory — which may result in higher levels of unsalable product returns. While it is not possible to quantify the potential impact on unsalable returns volume with currently available data, a simple illustration of the economics underscores the potential incremental cost. Even a 1% increase in return volume would add $60 million to $80 million in annual product costs for supply chain stakeholders (not including the additional costs associated with processing, handling and disposal).
While implementation of unit-level traceability has presented major challenges and changes, “the use of standardized product identifiers, serialization of products and the possibility to link critical data elements may present opportunities to improve regulatory compliance and adherence,” the report says. “For example, stakeholders may be evaluating whether manufacturers will be able to identify, by individual product serial numbers, which wholesale distributors (or other entities) have received specific recalled product.
“It is hoped that this ability to better target recall efforts and associated communications will boost recall adherence and reduce unnecessary or additional labor costs.”